With Formex Plastik GmbH as part of the WALTHER Faltbox Group, we can look back on more than 55 years of experience in plastic injection moulding technology.
Our production at Formex in Kevelaer
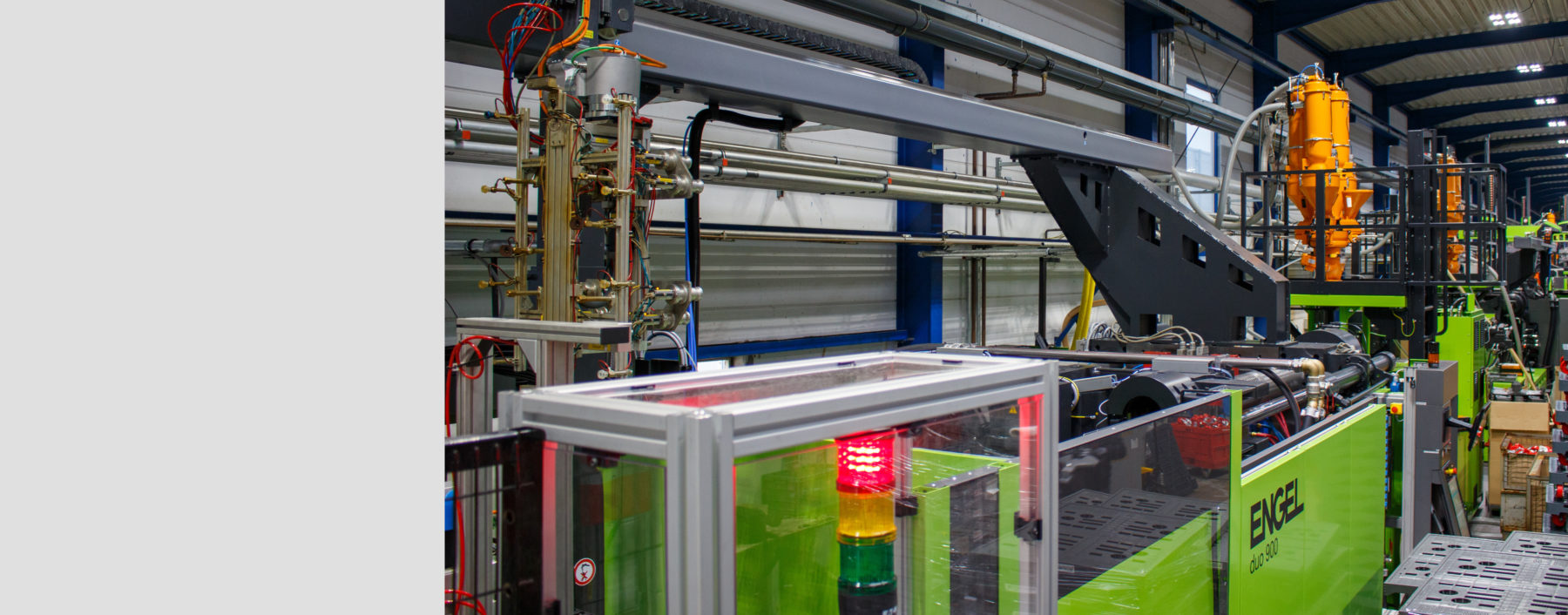
Formex Plastik GmbH
Our production
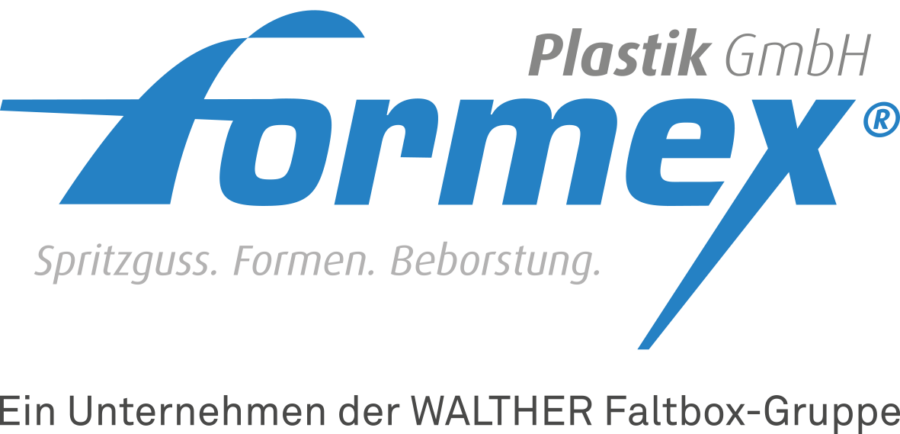
The complete supply chain from a single source
We have been manufacturing our plastic products in Kevelaer since 1978. Together with Formex we designed and manufactured the first folding box. More than 45 years later, we offer the complete supply chain, from the first idea for a reusable product to series production in the millions, and as WALTHER Faltbox group we will continue to inspire the market with innovative reusable solutions! We very effectively match customer wishes and requirements to the technical possibilities offered by plastic as a material for reusable load carriers. Our communication channels are short - thanks to our own toolmaking department, alterations can be implemented quickly and we can respond to changes without delay.
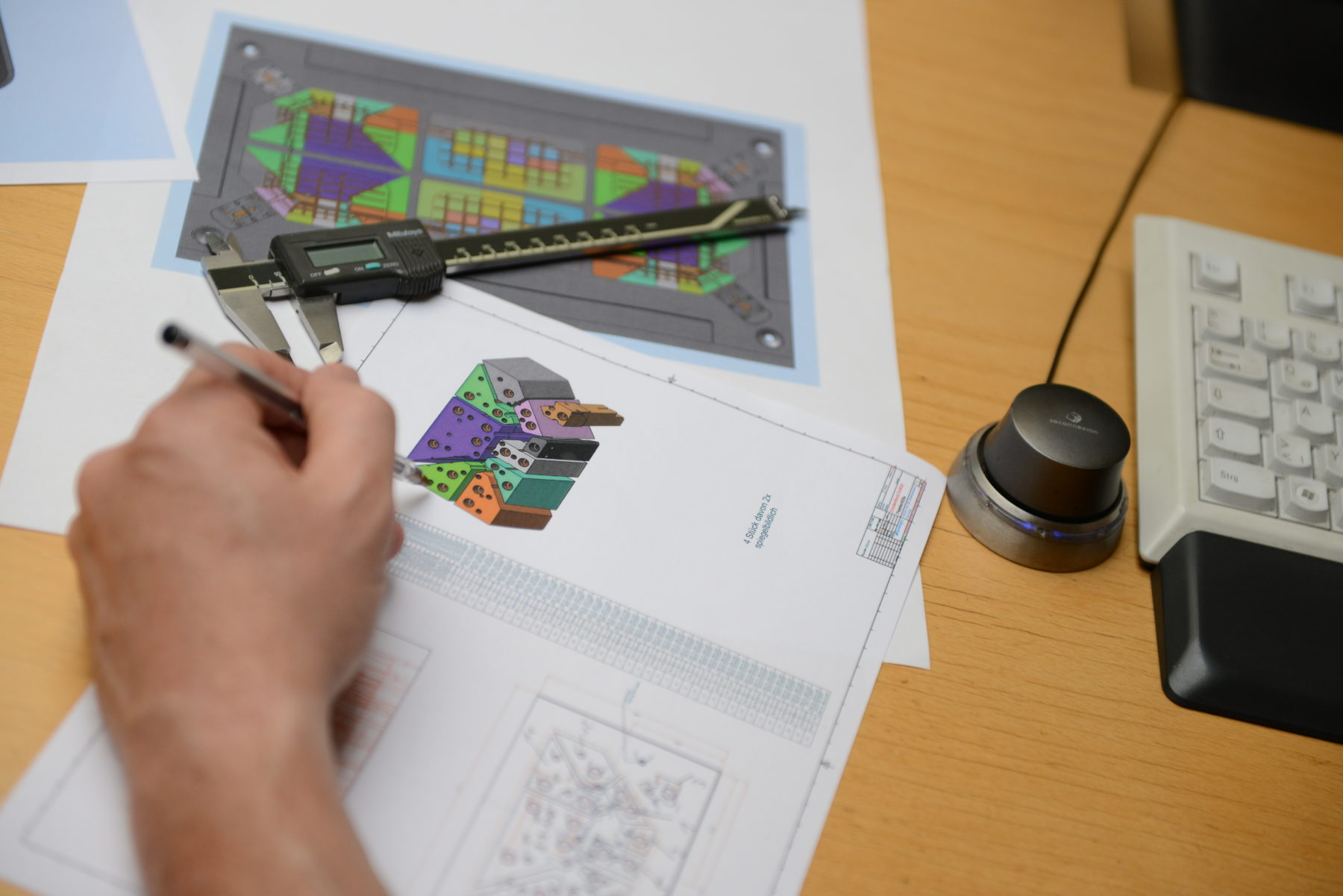
Our expertise
Innovation
We stand for creative ideas and new logistics solutions. We can draw on our wealth of experience gained in 45 years of successful work and our knowledge of markets and mechanisms. The right mix of experience and dynamism is our recipe for success.
Time-to-market
With integrated teams from the areas of sales, design, construction, toolmaking and production, ideas can be tested and implemented both very quickly and comprehensively. This allows know-how from all areas to be incorporated into further considerations and detailed planning.
Quality
Our principle of "everything from a single source - from the initial idea to the finished series container" reduces inefficiencies and teething troubles and maximises performance for our customers.
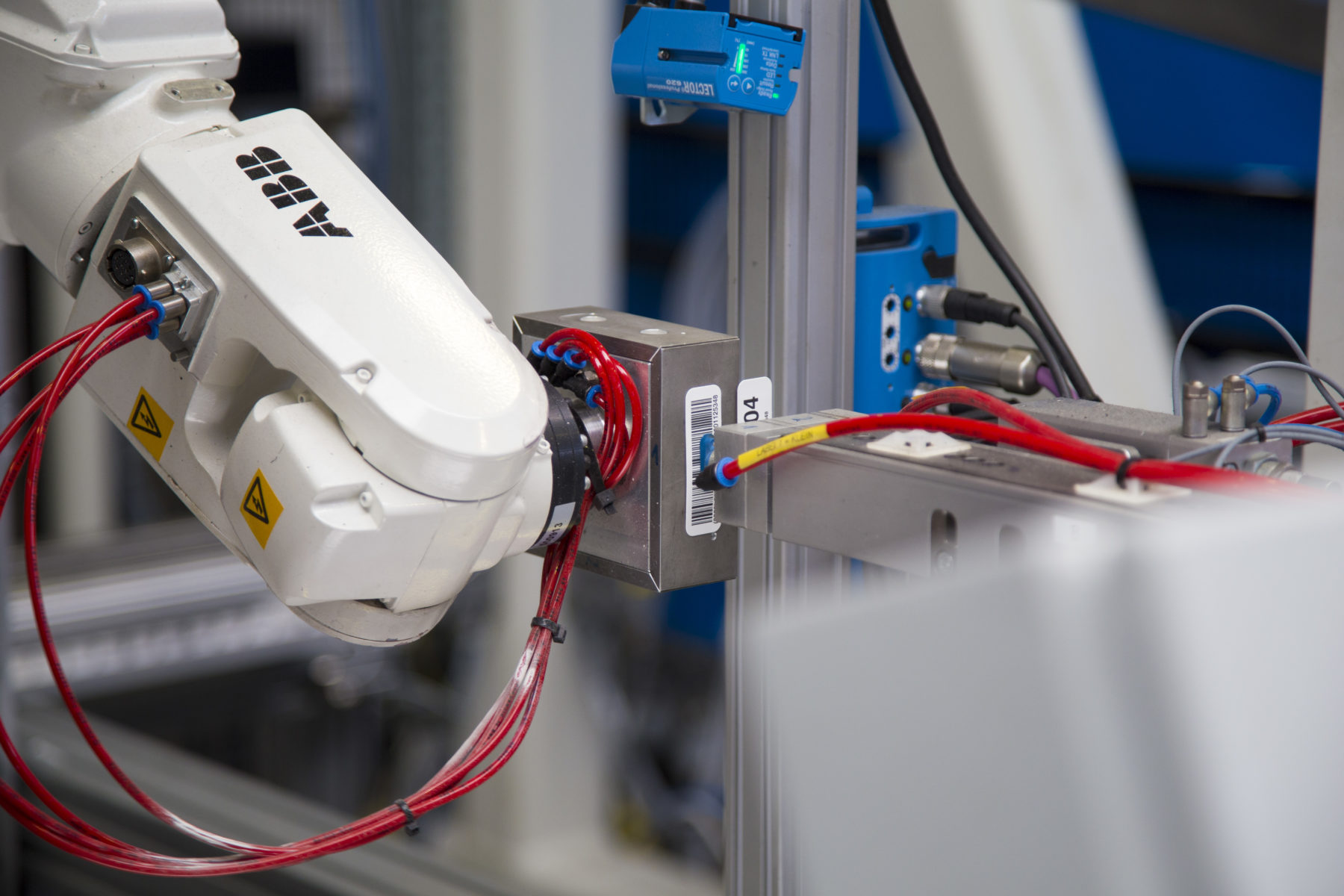
State-of-the-art equipment
We use state-of-the-art injection moulding machines and high-end injection moulding tools to produce high-quality and durable load carriers. This means we can supply customers with as many as several million containers a year.
Our moulds are based on a sophisticated modular design that allows us to adapt our products to customer requirements. This facilitates a wide variety of configurations so that the load carrier meets all requirements.
In production, robots and peripheral equipment ensure the automated handling of the individual parts. There are complex links between these systems: From fully automated assembly to synchronised production of all necessary components for a product, we have established a number of processes. Quality testing is firmly integrated in these processes. The production process, for example, integrates automatic inspection of the labels with scanners or monitoring of the printing by means of a camera.
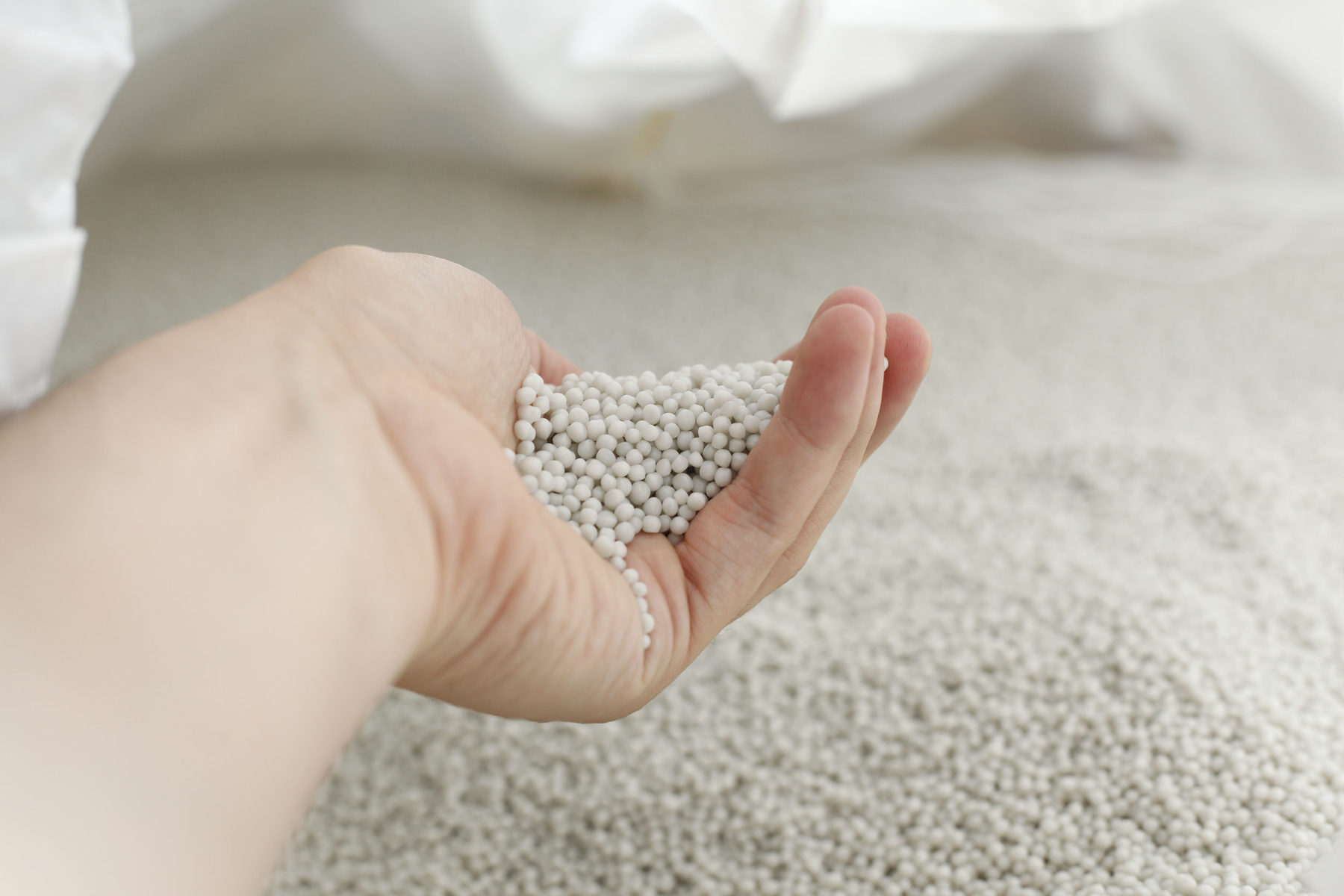
Saving resources
In addition, we use special software for injection moulding tools to digitally record and monitor machine data in real time. This allows the status of the moulds to be viewed at any time in order to proactively control the processes.
Particularly in energy-intensive production, we also consider saving resources and use state-of-the-art servo-hydraulic machines from ENGEL. Their ecodrive concept and the electric dosing unit drive considerably reduce energy consumption in production. That way, the machines make a significant contribution to sustainable and efficient production.
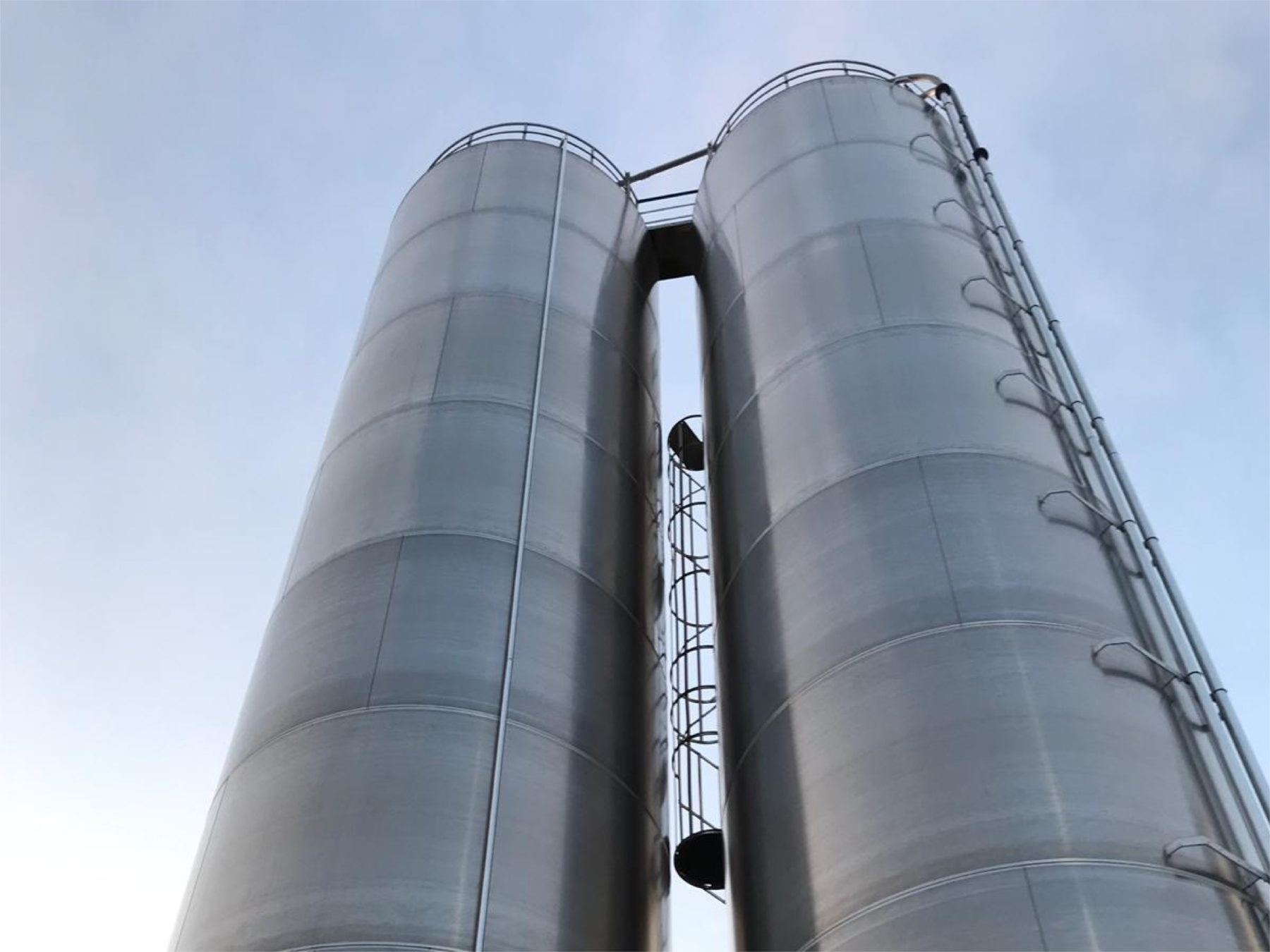
Granulate storage
Plastic granulate is the most important raw material for our products. The Formex premises include ten large silos with a height of 25 metres - and a total capacity of 2,000 tonnes. This ensures the necessary planning reliability for both us and our customers. And even if there is a shortage of raw materials or supply bottlenecks, production is always secured.
From the silos, kilometre-long pipe systems convey the granulate to the injection moulding plant. This is not only efficient, but also environmentally friendly, as no granulate is released into the environment.
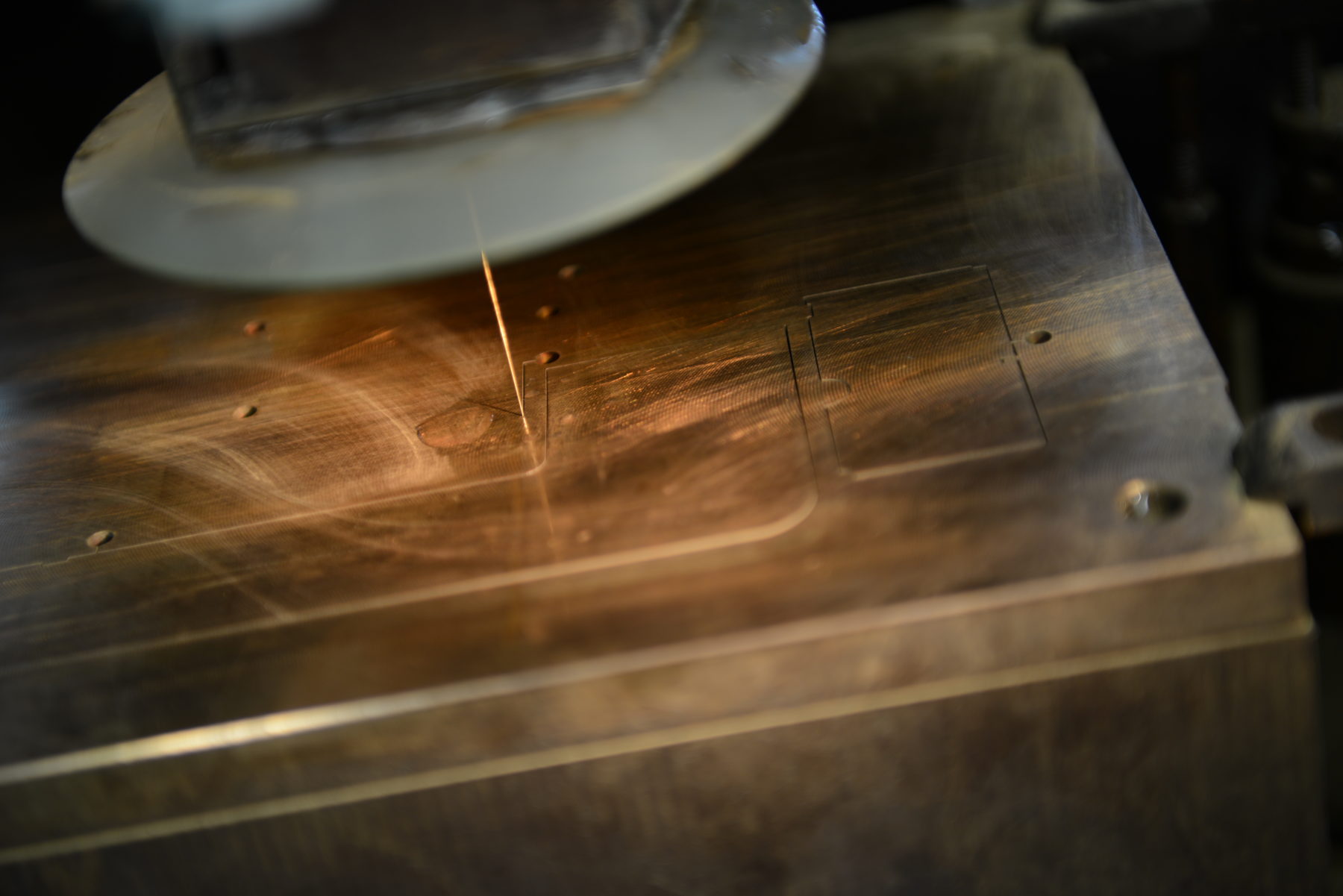
Toolmaking
Experienced specialists work in our toolmaking department and we have all the machining processes required for the production, repair and modification of modern injection moulds. Due to our proximity to production, we guarantee optimal support for the tools used as well as very short response times if maintenance or repair is required in the production process.
Whether in the support of existing moulds or in the production of new moulds based on customer requirements: our toolmaking department always gives its best to achieve optimum results. To ensure this at all times, our toolmaking department uses all common metalworking techniques. In addition to machining on CNC machining centres, our facilities include die-sinking and wire-cut EDM machines as well as a deep-hole drilling machine. Two specially equipped work areas for large and small tools are available for assembly, disassembly and conversions.
When toolmaking actually begins with the execution of the work, a great deal of preparation has already taken place behind the scenes. In the in-house design department, experienced engineers ensure that the individual work steps are well thought out and optimally prepared.
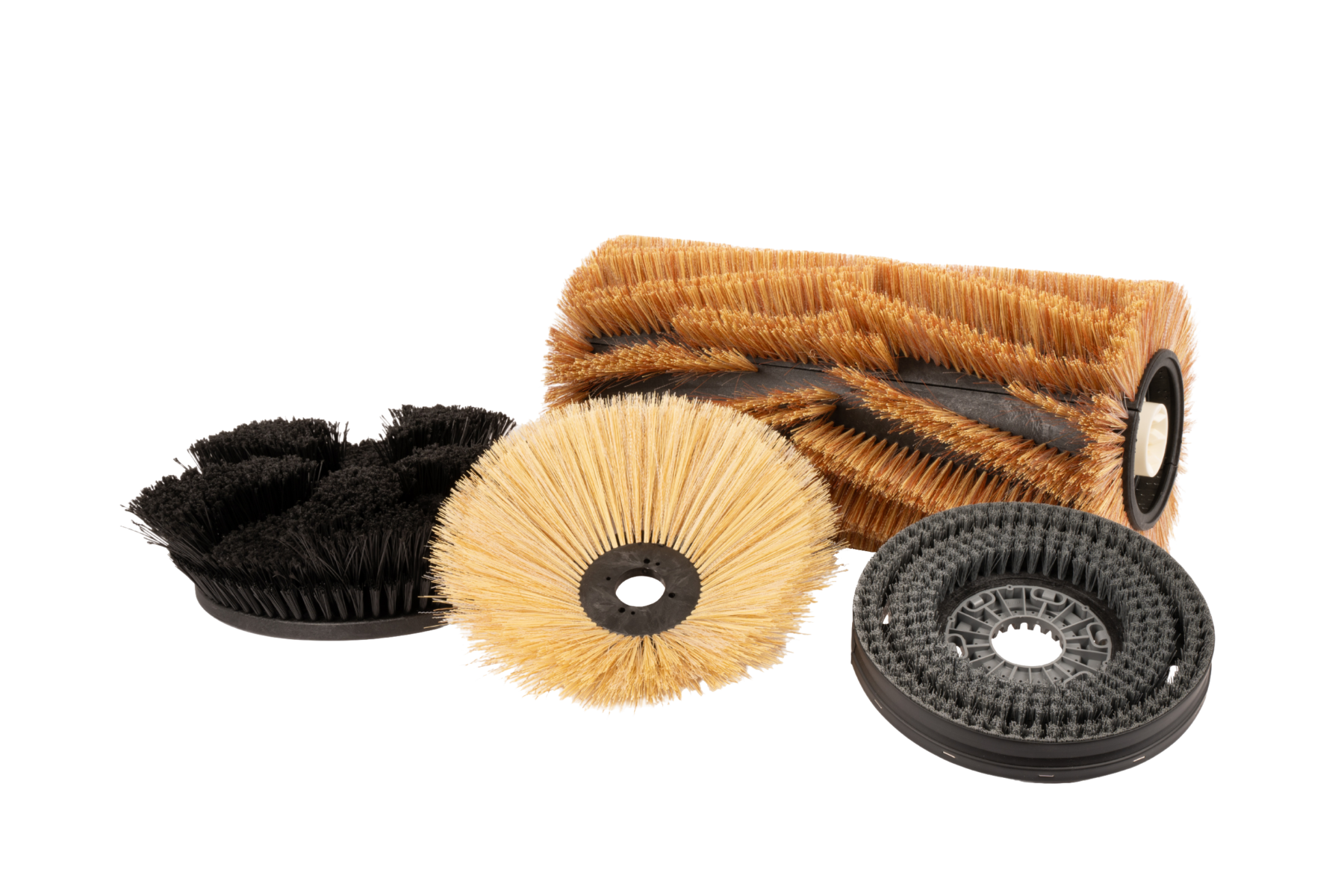
Brush production
In addition to injection moulding, we also have our own brush making department that meets even the high demands of technical brushes. Our vast machinery includes a wide range of brushmaking machines enabling us to fit bristles to almost any base body from our injection moulding production. Since we produce base bodies in house, we are able to realize any product idea, no matter how unusual.
The bristle determines the cleaning result. Not only the bristle material used is crucial, but also its quantity and, above all, its correct arrangement. Our highly specialised machines process any desired bristle material and are at the same time customised for one brush shape. Whether sweeping roller or disc brush: We have the right machine for every application.
Contact us now!
Do you have any questions regarding our production?
Then get in touch. We will be happy to answer your questions about our production.
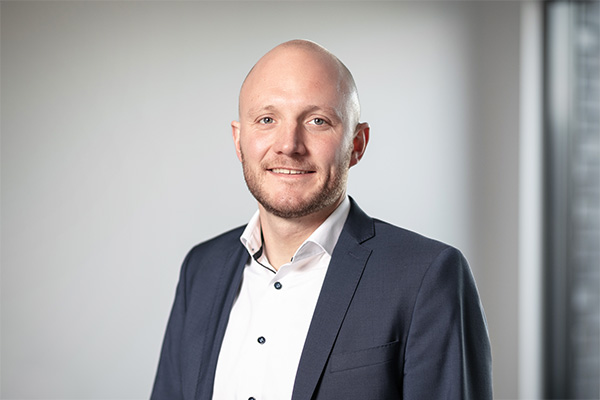
Andre Peters
Managing Director Formex Plastik GmbH
WALTHER Faltbox group
Our production
Find out more about the production of WALTHER Faltbox group in Kevelaer on the Lower Rhine.